Cell therapy offers transformative potential to treat and even cure diseases that were once considered untreatable.
However, high costs and supply chain challenges remain significant barriers to its widespread adoption. Breaking down these barriers requires more than incremental improvements. It demands a strategic shift in how cell therapies are manufactured, starting with smarter technologies and strategic facility designs that support production.
PM Group experts, Charles Heffernan and Daryl Kern, talk about the challenges and strategies for success.
The Cost Barrier: a strategic and operational risk
Manufacturers face the challenges of high capital expenditures (CAPEX) for facility build-outs and significant operating costs (OPEX) tied to manual labour, facility maintenance and legacy processes.
Concurrently, the variation in current manufacturing processes introduces risks to the reliability of supply. Manual handling increases the potential for batch failures, slows throughput and limits the ability to scale effectively. Combined, these factors directly affect patient access, regulatory approval and long-term commercial viability.
Smarter manufacturing choices
One of the most effective levers for reducing cost and enhancing robustness, lies in the adoption of closed, automated manufacturing platforms. These technologies eliminate many of the inefficiencies and risks associated with traditional manual processes.
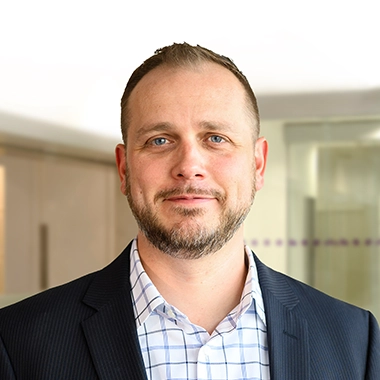
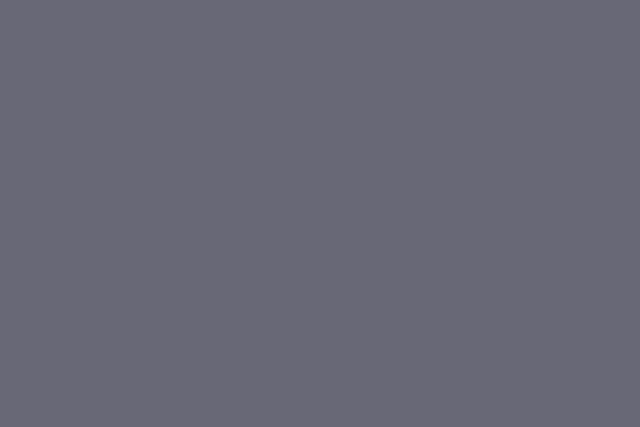
“Closed systems such as isolators, Automated Processing Units (APUs) and Robotic Processing Units (RPUs) minimize contamination risk."
Daryl Kern
Director of Architecture, USA
"They improve consistency and allow for more streamlined facility layouts. They can also reduce cleanroom classification and size, reducing both construction and operational costs,” says Daryl.
Semi-automated platforms, while less advanced, offer a valuable interim step by integrating automation into select process stages. This allows manufacturers to phase in modernisation while still achieving measurable gains in efficiency and reliability.
Lower capital investment
These scenarios measured total cost of ownership including CAPEX and OPEX, labour needs, facility size and scalability across different levels of automation and system closure. The findings were compelling.
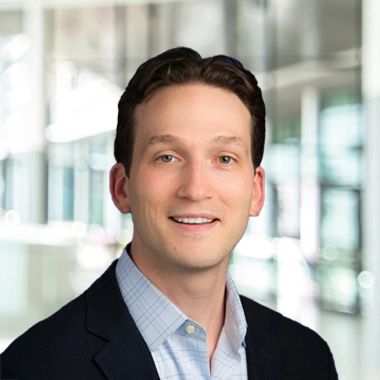
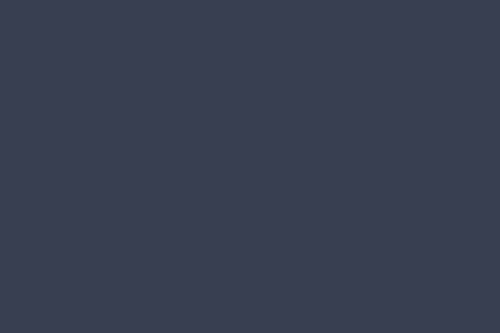
“Transitioning from open, manual systems to closed, automated platforms delivered an estimated 45% reduction in total manufacturing costs."
Charles Heffernan
Director of Advanced Therapies and Biologics
In some cases, the capital investment achieved payback in less than one year - demonstrating a clear return. Beyond cost, these platforms are expected to show improved outcomes across key operational metrics. These include:
- speed to market
- flexibility
- scalability
- supply chain robustness
The same learnings are also being applied to design fully automated QC labs of the future. The result is a comprehensive solution for forward-looking manufacturers.
Cost enables access
Reducing cost is not an end unto itself. It is a necessary condition to support scaling and enabling broader global distribution. By adopting technologies that lower the total cost of ownership and improve operational resilience, manufacturers are better positioned to meet both patient and payor demand as well as comply with regulatory expectations.
Cell therapy is entering a critical phase of growth. The therapies are here. The challenge now lies in delivering at scale efficiently, reliably and affordably.
By investing in smart manufacturing technologies today, companies can future-proof their operations while fulfilling their mission: expanding access to life-changing therapies for the patients who need them most.
Ready to Build Smarter? PM Group can help to optimize your cell therapy manufacturing strategy - from facility design to operational readiness.