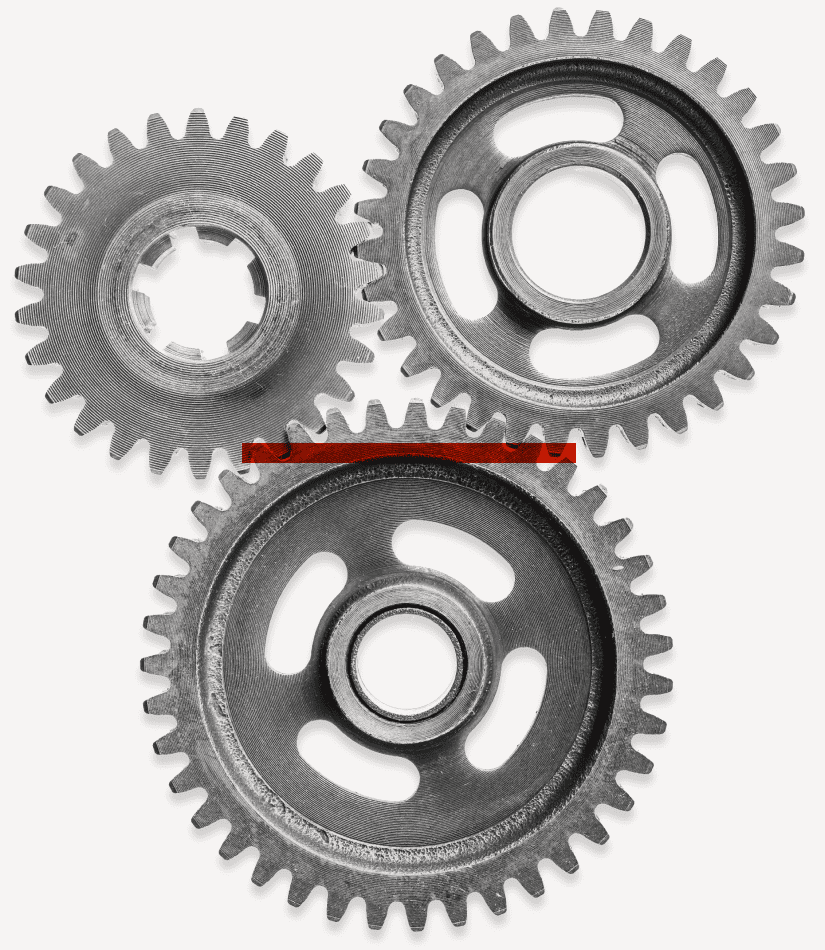
404:
Sorry, we can't find that page
We couldn't find the page you're looking for, but don't give up! You can try going back to the previous page or click on the "Take me home" button to return to our homepage.
We couldn't find the page you're looking for, but don't give up! You can try going back to the previous page or click on the "Take me home" button to return to our homepage.